热交换器的尺寸测量
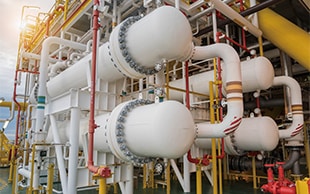
热交换器是工艺的热交换中不可或缺的装置。例如,在日本国内的石油化学工艺中,安装了大量热交换器,作为石脑油热裂解装置(乙烯装置)。
热交换器根据目的有各种类型,下面以工艺中常用的多管式(管壳式)热交换器为中心,说明结构、类型等尺寸测量所需的基础知识。此外,还介绍尺寸测量的要点和难题,以及利用新款测量仪解决难题的方法。
什么是热交换器
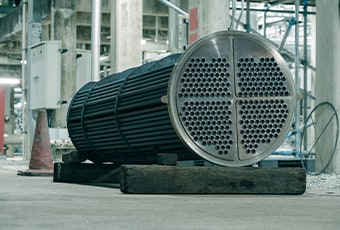
热交换器是将热量从热的物体传导至冷的物体的装置。不论是固体、液体还是气体,物体的热量都具有从高温转移到低温的性质。热交换器是利用该性质高效转移热量的装置,一般使用液体作为传导热量的介质。
热交换器的类型和结构
热交换器可根据结构和流动方式等进行分类。根据结构分类时,大致可分为管式和板式。管式有多管式、单管式、双管式等。板式有平板式、螺旋板式、夹套式。
其中多管式热交换器也被称为“管壳式”,可在狭小空间内获得较大的传热面积。此外,还能减小流体的压力损失,因此多用作工艺的热交换器。
下面将说明多管式热交换器的类型和结构。为了准确地测量尺寸,了解各热交换器的结构特点十分重要。
多管式热交换器的类型
多管式热交换器有3种,即固定管板式、浮头式、U形管式。
固定管板式热交换器
固定管板式热交换器的管体通过扩管或焊接,安装在固定于壳体的管板上。它的优点是结构简单、能以低成本制造。不过由于壳体无法清洁,不适合用于将脏污较多的流体或腐蚀性流体流向壳体侧的热交换。另外,还需要注意壳体和管体的热膨胀,当壳体侧和管体侧的流体温度差较大时,壳体需采用伸缩接头。
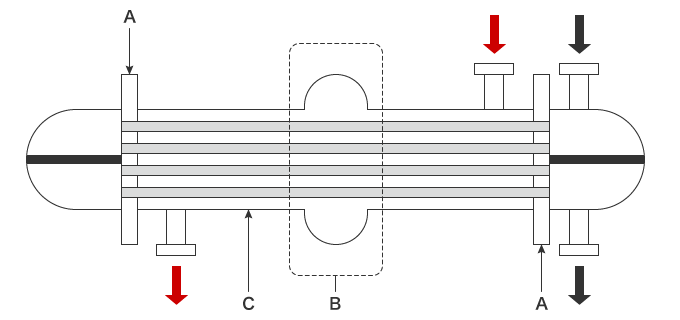
- A
- 管板
- B
- 伸缩接头
- C
- 壳体
- 黑色箭头
- 管体侧流体
- 红色箭头
- 壳体侧流体
浮头式热交换器
浮头式热交换器管束的一侧安装在管板上,另一侧通过扩管或焊接,安装在浮动管板上。壳体与管束未接合,因此壳体与管束具有对于热膨胀能够自由调节的特点。此外,由于管束容易装卸,可进行清洁、检查、修理等维护工作。
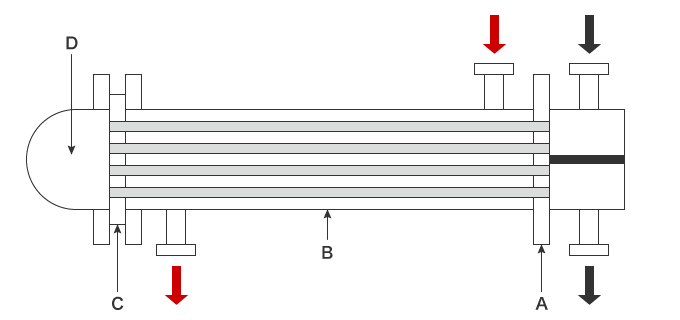
- A
- 管板
- B
- 壳体
- C
- 浮头管板
- D
- 浮头
- 黑色箭头
- 管体侧流体
- 红色箭头
- 壳体侧流体
U形管式热交换器
U形管式热交换器将管体弯曲成U形插入壳体。壳体与管体未接合,因此与浮头式热交换器相同,壳体和管体对于因热膨胀而发生的变形能够自由调节。此外,管束可装卸,便于实施维护,但管体的U形部位不易清洁。
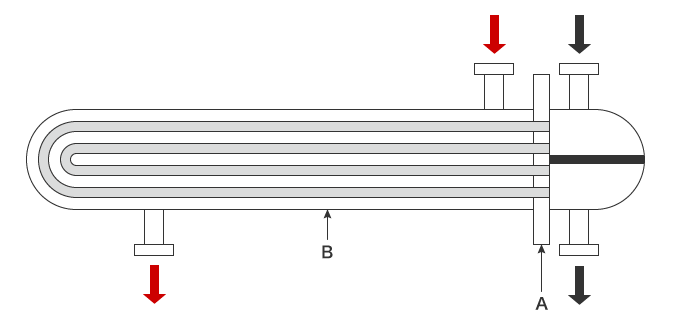
- A
- 管板
- B
- 壳体
- 黑色箭头
- 管体侧流体
- 红色箭头
- 壳体侧流体
多管式热交换器的结构
这里将以浮头式热交换器为例,介绍多管式热交换器的结构。浮头式热交换器由浮头(壳盖)、垫圈、壳体、管板、分隔室(通道)、管束等构成,在测量热交换器尺寸时,预先了解这些部件的位置和作用是很重要的。
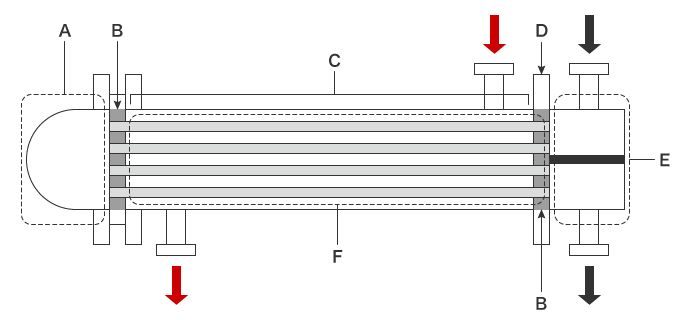
- A:浮头(壳盖)
- 浮头是将圆帽状的头部焊接在法兰上的部件。通过法兰接合至壳体。
- B:垫圈
- 垫圈是用于提升通道盖(分隔室的盖子)、通道法兰和管板之间、壳体法兰、壳体和壳盖等气密性的部件。
- C:壳体
- 壳体是容纳用于交换热量的管束的部分。
- D:管板
- 管板是支撑管体、分隔壳体侧流体和管体侧流体的部件。安装在管板上的管体,安装部分会实施扩管,获得高度气密性,防止流体发生泄漏。
- E:分隔室(通道)
- 分隔室是管体侧流体的出入口,也称为“通道”。
- F:管束
- 将进行热交换的管体聚集成束的部件。管束大多由管板、管体、挡板等构成。
黑色箭头:管体侧流体
红色箭头:壳体侧流体
热交换器尺寸测量的必要性
多管式热交换器内极为重要的部件是管束和法兰。管体是在热交换器内进行热交换的部件,多根管体以高密度收纳在管束内。因此,尺寸和形状稍有误差,就会产生应力。法兰是用于接合各部件的部件,其尺寸精度对气密性有巨大影响。
下面将说明热交换器各部位尺寸测量的必要性和理由。
管体和管束
管体使用被称为“热交换专属钢管(热传导专属钢管)”的钢管。热交换专属钢管分为被称为“无缝钢管(无接缝钢管)”的没有接缝的管体和“电阻焊钢管”。热传导专属钢管常用于伴随着承受高温、高压危险的用途,因此按照材质,设定了严格的设计条件、尺寸精度、检查基准。
然而当通过焊接将管体接合至管板时,可能会因焊接而产生应变。大型热交换器的管体全长为数米,管束直径超过2 m,管束内必须以高密度装入小口径的管体。同时,管体会随着高温或低温产生的热量变化而伸缩。
因此,必须严格测量管体的尺寸精度,并需要在扩管部检查因焊接而产生的应变和焊点。此外,管束和壳体之间的间隙较小,所以管束完成形状的尺寸测量也必不可少。
法兰
法兰通过垫圈夹住各部件,将部件彼此接合,获得气密性。因此,低精度的形状和尺寸会引起流体泄漏。例如,当法兰座出现应变时,垫圈受力不均匀,无法实现设计中要求的气密性。另外,如果法兰面对于轴方向的角度不符合设计要求,不仅会安装困难,还会因为法兰固定螺栓的紧固力使法兰发生变形,强度大幅下降。
出于以上原因,法兰的形状和尺寸,特别是承受压力高的部分,要求具有高精度。不仅在制造时,在进行管体更换和清洁等维护时,尺寸测量也是必不可少的。
热交换器的尺寸测量
将说明多管式热交换器的尺寸测量要点。
尺寸测量要点
多管式热交换器内极为重要的测量要点是管体和法兰的形状和尺寸。
下面将说明这两个部件的尺寸测量要点。
管体和管束
除管体的全长和外径之外,表示管体轴中心偏移的同轴度、安装于管束后的管体间平行度等也是重要的测量要点。
将管体安装至管束时的管体间距由管体外径决定。管体外径为19 mm(3/4 in)时间距为25 mm,外径为25.4 mm(1 in)时间距为32 mm,间距不低于外径的1.2倍。此外,必须将长度为3 m(10 ft)或6 m(20 ft)等的长管体以高密度收纳在管束内。管体的尺寸和形状稍有误差,就会在组装管束时,在各部位产生应力,因此特别需要高精度测量。
法兰
在法兰的尺寸测量中,法兰面对于法兰轴方向的角度、直角度和平面度等均为重要的测量要点。
法兰夹住垫圈,通过螺栓将部件彼此接合。法兰上因螺栓而产生强力的紧固扭矩,通过该力按压垫圈,实现气密性。此时,如果法兰的角度对于轴方向不是正确的角度,紧固扭矩可能会变得不均匀,导致垫圈部分破损或法兰变形。而且当法兰面有起伏等时,会无法充分地按压垫圈。法兰的尺寸和形状误差会导致垫圈嵌合不良,从而造成流体泄漏等严重故障,因此需要仔细测量。
热交换器尺寸测量的难题和解决方法
对于大型热交换器,除成品外,确认制造期间的加工精度以及更换部件时的组装精度也十分重要。进行这些测量时多采用千分表、卷尺、大尺寸游标卡尺等。个别构成零件也常常是大型尺寸,一般至少需要2至3人进行测量。而且此类方式存在一些难题:测量人员不同造成的测量值偏差、应变趋势等不易掌握、测量耗时久等。
为了解决这些问题,越来越多的人开始采用新款三坐标测量仪。采用基恩士大范围三坐标测量仪“WM系列”,能通过无线探头,以高精度测量大型热交换器的尺寸。在测量范围内,可自由接近工件深处部位,只需探头接触的操作,即使单人也能轻松测量。而且与千分表、卷尺、大尺寸游标卡尺等测量器具相比,测量结果无偏差,可进行定量测量。
管体的全长、角度、平行度
短管体的长度大多采用3 m(10 ft),长管体则采用6 m(20 ft)。如果要用卷尺测量,至少需要2名作业人员,每次实施测量得到的值不尽相同,难以进行准确测量。例如,管体的平行度需要移动千分表来测量。但是,测量值会随着千分表接触角度和强度而变化,所以作业人员不同会令测量值发生偏差。而且,必须在指定的轴线上反复测量,测量作业会持续很长时间。
采用“WM系列”,只需将探头接触测量点即可测量。平行度和各部位角度,也只需用探头接触管体的基准要素和目标要素,即可完成测量。单人也能快速测量,不会因为作业人员不同而导致测量值偏差。此外,还可以快速确认公差值相对于设计值的判定。
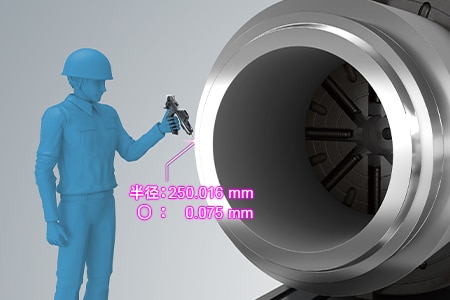

管板各部位的尺寸和平面度
大型热交换器的管板直径长达数米。若需用千分表测量管板的平面度,与测量管体的平行度相同,必须移动目标物或千分表进行仿形测量。但是,要准确移动千分表或大型管板十分困难,不可避免地会产生测量误差。
“WM系列”采用便携式设计,可安装至各种地方,无需移动目标物。可在目标物附近安装测量仪,立即开始测量。无需移动目标物,只需用探头接触基准要素和目标要素的测量点,即可测量平面度。管板的高度差等各部位尺寸也能轻松测量。
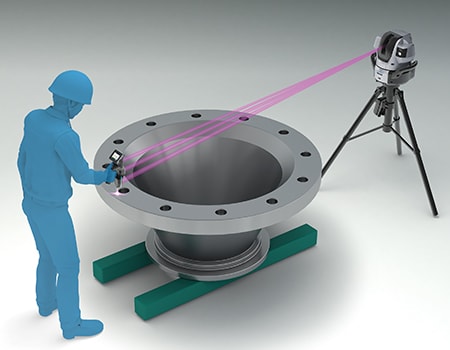
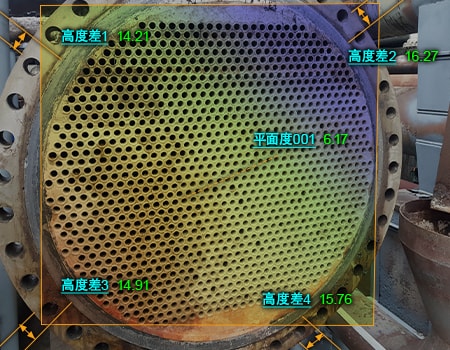
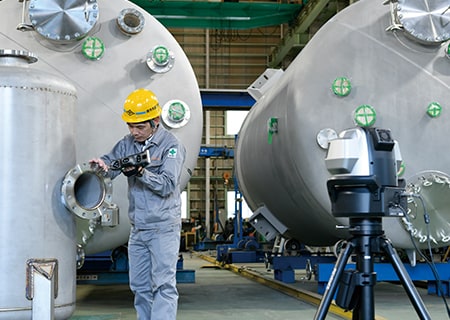
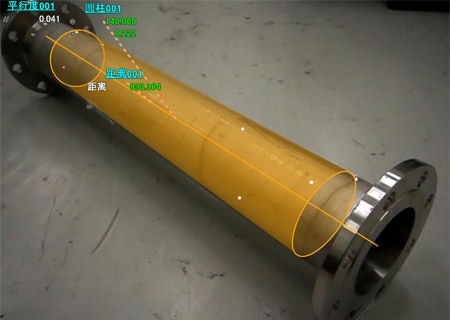
热交换器尺寸测量的高效化
采用“WM系列”,通过只需无线探头接触的简单操作,单人也能测量大型热交换器各部位的形状和尺寸。而且,除了之前的介绍外,还拥有以下优点。

- 可以高精度测量大范围
- 以高精度测量大范围区域,最大测量范围长达25 m。搭载“测量指南”模式,可存储测量步骤,测量相同位置,因此不会产生人为的测量数据偏差。
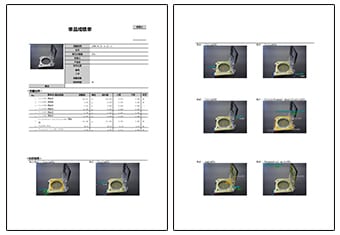
- 可保存自带照片的检测结果报告书
- 可自动制作带照片的检测结果报告书,测量位置一目了然。不仅有助于和客户建立信赖关系,还能以数字形式保存测量结果,从而提升公司内部数据管理的效率。
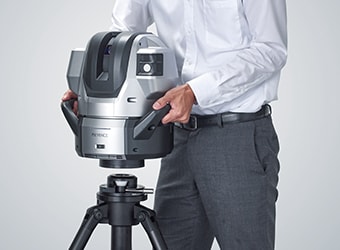
- 便携设计,可放置在现场
- 可把主机放入台车自由携带的便携规格。可携带至现场,当场立即测量施工状态。

- 可与3D CAD数据进行比对
- 可将测量目标物的形状与从3D CAD文件中读取的形状进行比较测量。与3D CAD数据之间的差异还可以显示在彩色图中,支持自由曲面和轮廓度测量。
“WM系列”不仅能测量大型热交换器各部位的尺寸和形状,还能强力支持与3D CAD数据的比对工作等。从大型热交换器的制造,到安装和质量管理时的必要工作,飞跃性地提升效率。