拉延加工件的厚度测量方法
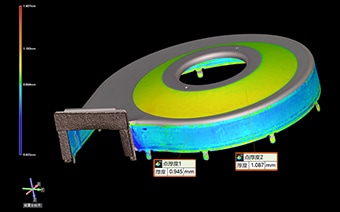
拉延加工是制造金属材料的杯子、盒子、厨房水槽等产品的冲压加工法。该加工被称为冲压加工中难度极高的加工方法,在加工期间由于应力和摩擦等,容易发生厚度误差、破裂等不良。因此,在加工后必须测量工件厚度,检查破裂、褶皱等缺陷。
因此,下面将说明拉延加工的主要类型以及拉延加工件的缺陷类型等。此外,还介绍接触式测量方法存在的课题及解决方案。
何谓拉延加工
拉延加工是将金属板成型的冲压加工的一种,成型产品由1块板材(坯料)制成,呈无接缝、带底的容器状。
用凹模和压边圈夹住坯料,并将被称为“冲压模”的模具压入,形成杯状或盒状。此时,压入深度超过冲压模半径的加工称为“深拉延”,由于坯料的材质和厚度等无法一次性压入进行加工时,分数次压入。
与需要切削、敲击等加工的切削加工和锻造加工等相比,拉延加工具有耗费工时少、可制作形状复杂的产品等优点。

- A
- 冲压模
- B
- 压边圈(按压褶皱)
- C
- 坯料
- D
- 凹模
拉延加工机的加压方式
拉延加工机大致可分为机械冲压机和液压冲压机两类。机械冲压机是将电机的旋转力机械性地传导至冲压模,从而施加压力的冲压机。液压冲压机是利用液压使冲压模滑动,从而施加压力的冲压机。
机械冲压机加工速度快,易于维护。不过,冲压模的可移动量固定,而且无法调节加压,因此不适合用于深拉延加工。而液压冲压机可调节加压,与机械冲压机相比,不仅拥有更长的冲程,还容易调节加工速度。同时具有不会发生过载等特点。然而,为了调节液压以及防止发生液压泄漏等,必须定期维护。
拉延加工大多使用机械冲压机实施加工,机械冲压机无法完成的拉延加工再由液压冲压机实施。近年来,由于实现了高精度加压调节,人们开发出配备了可自由运动的伺服电机的冲压机。
拉延加工的类型
拉延加工有圆柱拉延、方柱拉延、异形拉延等加工方法,另外还有用于加工复杂形状的拉延加工。下面将说明代表性的3种加工方法。
圆柱拉延
圆柱拉延是指将坯料成型为圆柱状的加工。这是基本的拉延加工,成型件呈杯子或碗状。

方柱拉延
方柱拉延加工是指将坯料成型为方柱状的加工。成型件呈矩形容器或盒子的形状。成型件的角部分容易产生裂纹和褶皱。

异形拉延
异形拉延加工是指成型为复杂形状的拉延加工。非圆柱和方柱形的燃料箱、罩盖、用于提升面强度的肋材等,也可通过异形拉延加工成型。

拉延加工的不良
下面将说明冲压加工中发生不良的类型和现象。冲压加工的不良有多种类型,此处将集中说明下图所示的代表性不良。

- A
- 破裂
- B
- 边缘褶皱
- C
- 褶皱、冲击线
- D
- 拉模
- E
- 回弹
破裂
坯料在成型后会硬化和脆性化。脆性化的部分会产生残留应力以及拉伸和压缩的不平衡,发生破裂。
- 破壁:
- 属于壁裂不良现象的一种。它是指在对薄板实施深拉延加工时,在角的立壁上发生的壁裂断裂。
- 漏底:
- 力集中在冲压模的R部,使接触面积小的部分发生开裂的现象。
- 边缘破裂:
- 由于凹模肩部的变形阻力超过坯料屈服点发生的破裂。
- 主体破裂:
- 在锥形拉延加工和半球形拉延加工中,固定坯料的力过强时发生。
- 放置破裂:
- 加工后经数日发生的破裂。材料因加工而硬化且脆性增大的部分受到残留应力的作用时发生。坯料上的小裂纹也是原因之一,常见于不锈钢和黄铜的加工。
褶皱
成型时对坯料产生的拉伸力和压缩力导致的不良。
- 口边褶皱、侧壁褶皱:
- 口边褶皱是发生在凹模R部的褶皱。侧壁褶皱是在凹模R部下方到侧壁的区域内发生的褶皱。这两种不良在拉延的间隙过大时发生。
- 主体褶皱:
- 在锥形拉延和半球形拉延中发生的不良。在凹模R部和冲压模R部存在坯料固定未起作用的部分时发生。
- 边缘褶皱:
- 边缘部发生的不良。坯料固定不充分时发生。
冲击线
在成型初期阶段用压边圈固定的坯料上承受张力,从而在模具R部发生的板厚度减小的损伤。
拉模
在凹模与材料间,加工油的油膜破裂,使凹模、冲压模接触坯料,由此产生的深度损伤。拉模在流动方向上呈线状发生,随着加工的进行而变得明显。
回弹
回弹是指成型件内部存在的残留应力导致成型后的工件略微恢复原来形状的现象。发生回弹时,会出现以下不良。
- 角度变化:
- 由于板厚度方向的应力差,导致弯曲部分的角度发生变化的不良。
- 壁面翘曲:
- 纵向应力差引起壁面翘曲的不良。
- 扭曲:
- 由于板厚度方向的应力差以及面内方向的应力引起整体扭曲的不良。
- 棱线翘曲:
- 由于板厚度方向的应力差,导致弯曲棱线翘曲的不良。
拉延加工的厚度测量课题
确认拉延加工件的厚度已获得期望尺寸(公差范围内)和形状是非常重要的。特别是整体壁厚以及凹陷处的最小厚度,这两点会影响到产品强度,因此要求高精度、定量的3D形状测量。
使用三坐标测量仪、游标卡尺等测量,但是存在用三坐标测量仪准确完成测量的难度很高、用游标卡尺测量会因为不同的测量人员而产生偏差等各种课题。
使用三坐标测量仪进行测量的课题

一般来说,如要使用三坐标测量仪测量拉延加工件的厚度,必须使探头前端的接触件接触目标物上想要测量部位的两面。
此时,需要将接触件准确地接触指定测量点。此外,若测量范围较大,可通过增加测量点来取得更多位置的测量值,从而提升测量精度。
但是在测量拉延加工件厚度时会存在以下课题。
- 为掌握整体厚度和最小厚度,必须测量很多点,所以需要花费一定时间,而且难以掌握整体的详细形状。
- 很难完成CAD数据与测量目标物的比对,需要输入设计值、公差,在进行CAD比较时费时费力。
- 在良品判定方面,只能针对测量结果(公差)判断是否为良品,难以通过形状比较来确定良品和不良品的差分。
使用游标卡尺、千分尺进行测量的课题
利用游标卡尺、千分尺等手动工具,可以非常轻松地测量。但是存在发生测量误差、测量值有偏差等诸多因素。
使用手动工具时,手按住测量位置的力(测量力)、测量位置偏差等各种度的把握因人而异。这会造成测量值发生偏差,难以实现定量测量。若待检测的面积很大,必须测量很多点,相当耗时,而且在某些情况下,还需切断样品。当形状十分复杂时,甚至测量本身都无法完成。
拉延加工的冲压加工件的测量课题解决方法
如果重新审视使用的测量仪所存在的课题,可发现某个共同点。那就是,对于立体的目标物和测量位置,总是在以点或线接触的同时进行测量。
为解决此类测量课题,基恩士开发了高精度三维扫描测量仪“VL系列”。以非接触的方式,以面为单位来准确捕捉目标物的3D形状。快速完成载物台上目标物的3D扫描,高精度地测量三维形状。因此,测量结果不会产生偏差,可简单、定量地实施测量。具体优点如下。
优点1:厚度测量简单
可自动计算指定部位的厚度,并用颜色显示差分。通过3色显示画面设定阈值,可在检测时判断OK/NG,以及比较良品和不良品的形状。此外,通过渐变显示画面,在试制时与设计数据相比较,可分析厚度趋势,便于对板厚度减小和厚度分布进行分析。


优点2:以面为单位扫描3D形状。无需切断,厚度一目了然
当使用三坐标测量仪和游标卡尺测量异形拉延加工后的、形状复杂的工件时,必须测量很多点,非常耗费时间。此外,因为是以点为单位测量,所以要测量3D形状尤为困难。
采用“VL系列”,只需将目标物放置到载物台上进行扫描即可。采用非接触方式以及无需定位,实现了以面为单位捕捉目标物整体的3D形状。可显示目标物整体以及测量各个部位的轮廓,所以能够将形状不良的部位及其详细数值等可视化,便于测量人员掌握情况。
而且,采用“VL系列”,还能在比较3D-CAD数据和已取得数据的状态下测量截面,不必切断工件。可以根据获得的3D数据,用颜色实现厚度状态的可视化。可采用非接触方式轻松完成厚度测量。通过观察切断部位轮廓的偏移,可及早发现回弹等缺陷,并采取加压调节等措施。


优点3:通过颜色显示与3D-CAD数据的差分
可将设计的3D-CAD数据和获得的数据进行比对,并用颜色显示差分,从而针对工件设计实现完成效果的可视化。如此,产品形状分析所耗费的工时便能得到大幅削减。
此外,还能根据可沿着各个方向旋转的3D数据指定要测量的方向,实施二维测量。这样不仅仅可以测量边缘形状,而且还可以执行只凭二维信息难以进行的测量,例如二维投影立体形状的测量以及根据基准进行的高度测量等。
(汽车刹车部件)


总结:对拉延加工件的厚度测量进行飞跃性改善和高效化
采用“VL系列”,可通过高速3D扫描,以非接触的方式迅速、准确地测量拉延加工件的3D形状。
- 无需定位。将目标物放置到载物台上,通过只需一键的简单操作,即可完成测量。
- 因为是以面为单位来捕捉,所以可掌握目标物整体上有缺陷的位置,并对各个位置进行轮廓测量。
- 还可完成3D-CAD数据与取得数据的比较测量,以及根据3D数据实施二维测量。
- 可用彩色图显示3D形状。可将一目了然的数据进行共享,顺利采取冲压缺陷的应对措施。
- 可为多个测量数据统一进行平面度公差等设定。此外,还可判断OK/NG品,共享取得数据并快速分析NG品。
从拉延加工的厚度测量到不良分析及不良应对措施,“VL系列”飞跃性地提升了拉延加工件必要工作的效率。