准确地测量树脂成型的嵌合部件的方法
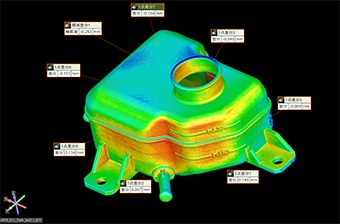
与金属和陶瓷器相比,树脂成型成本低,可大量制作高精度产品。与切削、冲压等加工方法相比,价格更低,量产性优异,因此在试制阶段使用铝等材料的部件,在量产阶段往往会更改为树脂材料。
但是,它也具有以下特性:成型时的粘度、温度和压力等异常导致射出和吹塑不良,以及模具磨损容易引起形状不良等。除此之外,由于树脂的特性,成型后仍然可能因为残留应力和热应力而引起变形。这些不良对于特别要求高精度的组装和嵌合部件来说是非常致命的,是直接关系到产品误动作、组装和嵌合不良的严重问题。
下面将介绍主要树脂成型方法、不良类型、开发和设计中的试制品测量以及防止在量产中流出不良品的测量方法。此外,还介绍接触式测量相关课题及解决方案。
何谓树脂成型
所谓树脂成型,是指将加热熔化的树脂注入模具,形成指定形状后冷却凝固,然后取出的加工方法。发挥各种树脂成型材料的特性,采用适合用途和形状的方法成型。
成型材料包括“热塑性树脂”和“热固性树脂”,前者使用将树脂制成米粒状的颗粒,通过加热产生可塑性,后者使用粉末状树脂,通过加热使其固化。有时也使用在树脂中混入添加剂和染色剂的颗粒或粉末,用以增强功能。
为了稳定地进行树脂成型,必须管理好模具温度、树脂材料的量、注入速度等成型条件。此外,还需要小心避免各工序中混入垃圾和灰尘以及静电引起异物附着。
树脂成型的类型
树脂成型的方法主要可分为射出成型、吹塑成型、挤压成型、压延成型,其中,射出成型和吹塑成型作为较具代表性的成型法被广泛运用。下面将说明这2种成型法。
射出成型
在射出成型中,将加热熔融的树脂注入并填充模具,使其成型。该成型法利用高压注入和填充树脂,因此壁厚较薄或形状复杂的产品也可高速成型,适用于大量生产。主要用于热塑性树脂的成型,偶尔也用于热固性树脂的成型。
(射出成型示例)

- A
- 料斗
- B
- 模具
射出成型的基本原理如下所示。
(1)从料斗投入材料树脂,加热熔融使其可塑化。
(2)使用模具等成型为一定的形状。
(3)冷却,凝固成模具的形状。
之后,从装置中取出成型件,经过各种工序和检测,成为树脂产品。用射出成型制作的主要产品如下所示。
- 智能手机套
- 电机产品的外壳和塑料模型
- 厕所的马桶座
- 汽车的保险杠和内饰面板
如上所述,从中小型产品到大型部件,该成型法用于多种多样的树脂产品的成型和量产,可谓非常具有代表性的树脂成型方法。根据制造的产品,射出成型可进一步分类为以下方法。
- 镶嵌成型:
- 该成型法预先在模具内埋入金属螺丝和端子等(镶嵌件),在其周围注入树脂,使其成型为一体(复合模塑)。
- 多色成型、异材成型:
- 该成型法将不同颜色或材质的树脂相组合,使其成型为一体。
- 薄膜内嵌成型、薄膜模内成型:
- 薄膜内嵌成型和薄膜模内成型称为“装饰性模塑”,用于树脂产品的商标和文字、电机产品的薄膜开关、汽车内饰(换档面板等树脂部件)的表面装饰。
薄膜内嵌成型是预先将印刷了花纹、光泽、哑光等效果的薄膜(装饰薄膜)设置在模具内,射出成型时利用热量和压力使模具内的薄膜与树脂贴合,成为一体的成型法。薄膜模内成型是在模具内设置装饰薄膜,在射出成型时将薄膜的装饰转印至树脂的成型法。
吹塑成型(中空成型、吹气成型)
吹塑成型将加热熔融的树脂挤压成管状,并用模具夹住,然后从内侧吹入空气,使其膨胀成型。适用于制造中空树脂成型件,根据制造方法,也称为“吹气成型”或“中空成型”。用吹塑成型制作的主要产品如下所示。
- 塑料瓶
- 液体化妆品、液体洗涤剂等的容器
- 配管
- 配管接头
填充液体时,有时需根据液体特性区分使用树脂。例如,当必须防止因氧气透过而发生氧化时,使用具有气体阻隔性的树脂。若要求具有耐化学品性,需使用含有不会因为化学品而变质的树脂的多种成型材料,并将其成型为层状。
根据制造的产品,吹塑成型有多种方法。下面将说明较具代表性的吹塑成型法。
- 挤压吹塑成型(直接吹塑成型):
-
挤压吹塑成型机的基本结构和原理如下所示。
[成型的流程] - A
- 型坯(热型坯)
- B
- 模具
- (1)挤压熔化树脂。
- (2)用凹模将圆柱状的型坯(热型坯)成型。
- (3)不待冷却和凝固,倒入模具内。
- (4)吹入空气,使其成型。
- 射出吹塑成型(射出拉伸/双轴拉伸吹塑成型):
-
射出吹塑成型机的基本结构和原理如下所示。代表性的产品有以聚乙烯对苯二甲酸酯(PET)为材料的塑料瓶。
[成型的流程] - A
- 拉伸杆
- B
- 模具
- C
- 预制件(冷型坯)
- D
- 加热器
- (1)预先将热塑性树脂射出成型为试验管状的预制件(冷型坯)。
- (2)加热预制件,使用拉伸杆将其伸入模具内。
- (3)吹入高压空气,使其成型。
- 多层吹塑成型:
-
为防止内容物发生氧化和变质,同时提升强度,型坯使用同时挤出气体阻隔性较高的乙烯-乙烯醇共聚物(EVOH)等制作成的材料。因此,该成型法适用于食用油、调味料、油箱等树脂容器的成型。
多层吹塑成型的基本原理如下所示。[成型的流程] - A
- 聚乙烯(PE)
- B
- 接合层
- C
- 乙烯-乙烯醇共聚物(EVOH)等
- (1)将2种以上的材料树脂同时挤出,使多层预制件(冷型坯)成型。
- (2)加热预制件(冷型坯)。
- (3)吹入空气,进行吹塑成型。
- 三维吹塑成型:
-
与将型坯纵向放入的挤压(直接)吹塑成型不同,可进行三维形状成型,避免材料自重下垂和毛刺出现。
该成型方法能以高品质制造具有弯曲部分或蛇腹状复杂形状的产品,如空调机软管、配管等。[成型的流程] - A
- 树脂吐出
- B
- 上下部闭合
- C
- 注入空气
- (1)用挤压机将树脂填充至储料器,将型坯成型。
- (2)从对侧出口吸引空气。使型坯沿着模具内的形状到达模具下部。
- (3)吹入空气,进行吹塑成型。
树脂成型件组装和嵌合不良的原因
与金属相比,树脂成型更容易加工,使用材料多种多样,可按需改变硬度和重量,自由表现颜色和形状。另一方面,材料温度和填充量稍有不同、模具有微小应变等,即会发生翘曲、起伏、应变、欠注等,造成组装不良和嵌合不良。
嵌合不良是指,在结合或组合树脂产品时尺寸不匹配,无法结合或形成缝隙的不良。若强行组装发生嵌合不良的部件,可能会导致部件破损,要求气密性的部件发生内容物泄漏。
翘曲和起伏
树脂成型件的翘曲和起伏是指工件如同弓一样弯曲的状态,也称弯曲或扭曲。此外,根据翘曲方向,分为顺翘和反翘。
另一方面,起伏是各个方向的翘曲复合形成的表面凹凸。树脂成型件发生翘曲和起伏主要有以下原因。
- 树脂收缩差
- 模具温度不均匀
- 流动方向造成熔化树脂收缩率不同


- 树脂收缩差:
-
若树脂因为腔体内的温度和压力偏差而产生收缩差,则会发生翘曲。腔体内树脂收缩大小与温度成正比,与压力成反比。因此,当1个工件存在较细部分和较粗部分时,较细部分温度低,收缩小,而较粗部分积聚了热量,收缩大。这种温度差在腔体内造成收缩差异,因而发生翘曲等变形。
- A
- 收缩大(较粗部分)
- B
- 收缩小(较细部分)
- 收缩大
- 收缩小
- 模具温度不均匀:
-
模具温度不均匀时,腔体内的树脂产生收缩差,发生翘曲。例如,模具各部分的冷却时间不同,使树脂收缩量形成差异,发生翘曲。
- A
- 收缩大(高温)
- B
- 收缩小(低温)
- C
- 模具
- 流动方向造成熔化树脂收缩率不同:
-
收缩率因树脂流动方向而异,因此发生翘曲或起伏。在树脂中掺入玻璃纤维等材料时,纤维会沿着树脂大量流动的方向取向。因此,树脂流动方向的收缩变小,垂直于树脂流动方向的收缩变大。这种现象称为“纤维取向引起的收缩各向异性”,翘曲因此而发生。
- A
- 玻璃纤维
- B
- 浇口位置
- 收缩大
- 收缩小
应变
树脂成型件的应变是工件整体发生扭曲或翘曲的现象,主要因残留应力而发生。树脂成型中的残留应力是指树脂成型件内残留的内部应变,有朝外侧方向上残留的力,即“拉伸残留应力”,以及朝内侧方向上残留的力,即“压缩残留应力”。
“拉伸残留应力”发生于用高压力向模具射出的熔化树脂在模具内从外侧开始冷却凝固(固化)的时候,是成型件内侧受到的朝着外侧拉伸的力。“压缩残留应力”是在成型或加工时施加在树脂上的压力想要向内侧压缩的力。

- 压缩
- 膨胀

- 拉伸
- 收缩
有残留应力的树脂产品不仅会因为收缩或拉伸而影响尺寸精度,还可能会在某些时候因为树脂产品的残留应力发生反应而导致变形和开裂,例如切削、磨削等机械加工时、熔敷等加热时,用涂装和溶剂进行加工和处理时。除制造和加工期间以外,还可能由于经时变化而发生应变,从而引起变形,需要特别注意。
因此,有时会采用名为“退火(退火处理)”的处理方式,用来除去残留应力。
欠注
欠注是指树脂未能到达模具腔体的每个角落,成型件的一部分是不完整形状的现象。
其主要原因有树脂在到达末端部分之前便冷却凝固导致成型件的一部分形状不完整的“流动前端固化”,以及树脂无法顺畅流入模具内的“空气积存(积风)”。

流动前端固化的应对措施有
・提升射出树脂的温度。
・加粗流道。
・增大保压压力或延长保压时间。
空气积存(积风)的应对措施有
・修改射出速度。
・提升腔体表面温度。
・修改流动模式。
树脂成型的嵌合部件的测量课题
确认树脂成型件已获得期望尺寸(公差范围内)和形状是非常重要的。尤其是复杂形状部件的嵌合部分会影响组装作业和密闭度,因此要求高精度、定量的3D形状测量。
使用三坐标测量仪、游标卡尺等测量,存在用三坐标测量仪准确完成测量的难度高、用游标卡尺测量会因为不同的测量人员而产生偏差等各种课题。
使用三坐标测量仪测量嵌合部件的课题


- A
- 目标物
- B
- 探头
一般来说,如要使用三坐标测量仪测量翘曲和起伏,必须使探头前端的接触件至少接触目标物待测量面角落的4个位置。
例如,测量板材时,通常测量6至8点。若测量范围较大,可通过增加测量点来取得更多位置的测量值,从而提升测量精度。
但是在测量翘曲和起伏时会存在以下课题。
- 因为需要以点为单位进行接触和测量,所以很难掌握目标物的整体形状。
- 如需进行多点测量以获得更多测量值,必须花费大量时间,而且难以掌握整体的详细形状。
使用游标卡尺测量嵌合部件的课题
利用游标卡尺等手动工具,可以非常轻松地测量。但是存在发生测量误差、测量值有偏差等诸多因素。
例如,使用游标卡尺进行测量时,手按住测量位置的力(测量力)、测量位置偏差等各种度的把握因人而异。这会造成测量值发生偏差,难以实现定量测量。此外,若是大面积的翘曲和起伏,则需要测量很多点,十分耗时。
树脂成型的嵌合部件测量的课题解决方法
如果重新审视使用的测量仪所存在的课题,可发现某个共同点。那就是,对于立体的目标物和测量位置,总是在以点或线接触的同时进行测量。
为解决此类测量课题,基恩士开发了高精度三维扫描测量仪“VL系列”。以非接触的方式,以面为单位来准确捕捉目标物的3D形状。最快1秒完成载物台上目标物的3D扫描,高精度地测量3D形状。因此,测量结果不会产生偏差,可瞬间实施定量测量。具体优点如下。
优点1:以面为单位扫描3D形状。翘曲和起伏一目了然
当使用三坐标测量仪和游标卡尺测量形状复杂的树脂产品时,必须测量很多点,非常耗费时间。此外,因为是以点为单位测量,所以要测量3D形状尤为困难。
采用“VL系列”,只需将目标物放置到载物台上进行扫描即可。采用非接触方式以及无需定位,实现了以面为单位捕捉目标物整体的3D形状。可显示目标物整体以及测量各个部位的轮廓,所以能够将形状不良的部位及其详细数值等可视化,便于测量人员掌握情况。
如此便可确认试验品的模具和成型条件等、查明量产品组装不良的原因并顺利采取应对措施。可获得定量测量的形状数据,有助于利用容许值(公差)的数值管理翘曲和起伏,或进行趋势分析。


优点2:通过颜色显示与3D-CAD数据的差分
可将设计的3D-CAD数据和获得的数据进行比对,针对工件设计实现实物的可视化。难以测量的工件,也可以将取得的数据与3D-CAD数据相比较,借此明确至今仍未发现的问题,因此在嵌合不良位置调查和原因追究中非常有效。
此外,还支持各种尺寸测量,通过精密测量有问题的位置的尺寸,可详细分析问题点。


优点3:可在不切割样品的情况下分析截面
难以测量的截面也可以非破坏性地形成截面,从而进行详细测量、分析。可根据3D形状数据自由设定基准面,并可从各个方向测量截面。


总结:对嵌合部件测量进行飞跃性改善和高效化
采用“VL系列”,可通过高速3D扫描,以非接触的方式迅速、准确地测量树脂成型件的3D形状。
- 因为是以面为单位来捕捉,所以可掌握目标物整体上有缺陷的位置,并对各个位置进行轮廓测量。
- 即使是橡胶、软质树脂等柔软的目标物,也能采用非接触方式,高精度地测量形状。
- 无需定位。只需将目标物放置到载物台上并按下按钮的简单操作,即可完成测量。
- 可用彩色图显示3D形状。可将一目了然的数据进行共享,顺利制定翘曲、起伏、应变、欠注的应对措施。
- 轻松实现多个测量数据的定量比较和分析。
- 可为多个测量数据统一进行平面度公差等设定。
- 可判断OK/NG品。可共享数据并快速分析NG品。
综上所述,从测量作业到不良分析及不良应对措施,“VL系列”飞跃性地提升了工作效率。