冲压件不良(毛刺、凹陷等)的原因、不良位置以及截面(断裂面)的观察
冲压加工广泛应用于各种产品的量产。特别在近几年,随着汽车电子控制技术的发展,不仅是车身和滑动部件,连日趋小型化、高密度化的电气部件和用于电子设备的金属部件也要求具有高精度、耐久性和可靠性。
下面我们将为您说明冲压加工的代表性不良及其原因和解决措施。此外,还将介绍可以高水平、高效地观察不良位置、断裂面的4K数码显微系统的应用案例,展示其在研发的试验、设计、试制、品质保证的检查等工作中发挥的重要作用。

冲压中发生不良及问题的原因和解决措施
冲压加工的种类
冲压加工一般使用被称为冲模和凸模的模具,以各种方法对材料施加压力,制作出目标形状。以下列举了冲压加工中采用的代表性加工种类。
- 剪切:施加超出材料破坏限度的力,进行加工(切断)。
- 弯曲:在材料的一个方向施加拉伸力,在另一个方向施加压缩力,使材料发生弯曲。
- 拉延:通过拉伸应力加工材料。
- 压缩:对材料施加压缩力进行加工。
冲压加工中代表性不良及问题的原因和解决措施
下面将说明各种冲压加工中产生的代表性不良及其问题的原因和解决措施。由于材料的性质、设计和加工原理,可能很难完全消灭不良和问题,但是需要采取各种解决措施,降低不良的发生频率,尽可能提高成品率。
- 毛刺
- 原因:在剪切加工中,由于凸模和冲模之间的缝隙(间隙)过大等原因而发生。
解决措施:把剪切面调整到板厚度的1/2至1/3,或者使该状态变得均匀。
各间隙条件下剪切加工后的材料截面结构图如下所示,下面将说明各部位名称和特点等。
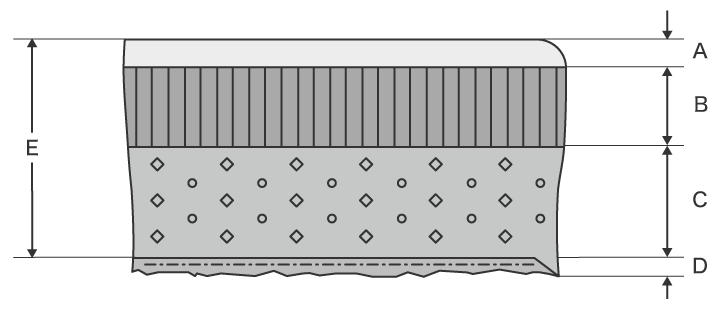
- 塌角:拉伸材料表面后变得光滑的表面。
- 剪切面:有纵向条纹的光泽面。凸模上的划痕、焊接金属与材料的摩擦会在剪切时造成细小划痕。
- 断裂面:像是被撕开一样,与剪切面相比,表面粗糙有明显的凹凸。
- 毛刺:从材料上突起,呈锯齿状。如果毛刺很大,在部件镶合等时可能会影响精度,或者发生尖锐毛刺伤人等安全问题,导致产品不良。
- 板厚
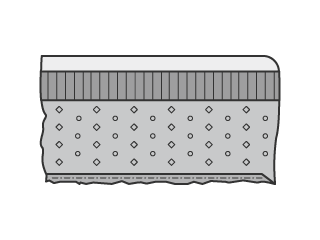
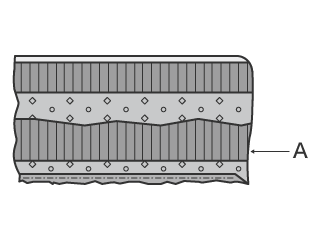
如果间隙超出合适的程度,间隙越大毛刺越大。此外,冲孔压力可能会造成翘曲(冲孔变形)等问题,降低形状和尺寸的精度。而一旦间隙过小,就会在断裂面的另一侧形成二次剪切面(右图中的A),产生胡须状的毛刺。
毛刺在金属材料的冲压加工中也被称作毛边,尺寸用毛边根部厚度(图中的A)和毛边高度(图中的B)来表示。
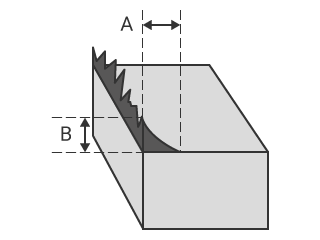
- 回弹
- 原因:弯曲加工后,残留在材料内部的压缩应力和拉伸应力会令材料回弹,增大加工部的弯曲角度。
解决措施:实施过度弯曲,弯曲至比目标角度更小的角度,除此之外,还可在凸模上设置一个突起,或者事先开一条V形槽,由此来防止回弹。
- 褶皱
- 原因:在拉延加工中,会向凸缘部分施加压缩力,因此产生褶皱。
解决措施:根据拉延条件使用“褶皱压块”,使材料受到的负载变得均匀。褶皱压块除了有固定式之外,还有利用弹簧和冲模垫的力的可动式。
- 开裂
- 原因:在拉延加工中,当拉伸力超出破坏限度时,材料发生开裂。
此外,在弯曲加工中,根据材料的压延方向和弯曲宽度尺寸,弯曲部分会产生裂纹(开裂)、裂缝、裂口。
解决措施:拉延加工中的措施有,降低褶皱压块的压力,或者使冲模的R形状变得平滑一些,减小变形阻力等。弯曲加工中的措施有,把弯曲线和材料的压延方向设置成直角,或者把弯曲宽度设置为板厚的8倍或以上等。
- 跳屑(凹陷、划痕等的原因)
- 原因:冲孔加工后,原本应该脱模的废料(冲孔碎屑)由于真空压力、油膜、磁性等附着在凸模上的现象。跳屑会造成材料表面出现凹陷或划痕等不良。同时,模具可能也会遭到损坏。
解决措施:在凸模上配备“顶料杆”,在废料和凸模之间设置物理缝隙。除此之外,还有从凸模前端排出空气,在凸模上开槽使空气进入,或者从下方吸走废料等方法。此外,还可采取降低使用油液的粘度、在凸模上开槽以减少油液接触面积等措施,减少废料吸附。
冲压件的截面及不良位置的观察案例
有时只靠生产现场的努力很难避免冲压加工中出现的不良。必须尽量在研发、材料选择、产品和模具的设计等初期阶段反复进行试验和试制,以达到改善的目的。而且,在品质保证方面,查明和改善冲压制作的金属部件的故障原因也十分重要。
因此,在这些阶段中不可或缺的操作是,通过显微镜仔细观察不良位置。
例如,在剪切加工中,可根据截面详细检查加工条件是否合适、是否会造成毛刺等。另一方面,因为金属加工件是立体的,所以整体对焦、视野内表面粗糙度和反射率不同等高难度观察要求也成了需要解决的课题。
下面我们将为您介绍4K数码显微系统“VHX系列”的优点,和使用它从冲压件的截面高精细地观察塌角、剪切面、断裂面等表面的细微差异以及毛刺、凹陷等不良位置的外观的案例。
冲压件截面(塌角、剪切面、断裂面)的高精度观察
在经过剪切加工后的冲压件截面上,可根据剪切面对于板厚的比例,评价凸模和冲模之间的间隙是否合适等加工品质以及毛刺产生原因等。截面上显现的塌角、剪切面、断裂面分别具有各自不同的凹凸、粗糙度、纹路等表面状态。此外,各部分颜色相同,对比度低,而且可能会由于光线反射率不同而在某些部分产生光晕,这些决定了要观察整体表面状态十分困难。
4K数码显微系统“VHX系列”配备了兼顾高分辨率和大景深的HR远心镜头、4K CMOS等,实现了超高的分辨率和图像解析度。因此,可获取截面整体对焦的清晰图像,并在图像上观察各种表面状态。
此外,新观察方法“Optical Shadow Effect Mode”,组合了专为此种情况设计的光学系统、4K CMOS和照明,借助多方向的照明分析拍摄的位移(对比度)。这样就可以高对比度清晰地观察微小的凹凸等表面状态。另外,还可在Optical Shadow Effect Mode图像上合成颜色信息,用不同颜色显示凹凸(深度和高度)信息,达到可视化的目的。
“VHX系列”通过简单操作实现这些先进的观察方法,使需要耗费大量时间设定条件的截面观察和评价,得到速度方面的提升。


观察微小毛刺的全幅对焦
即使冲压件中产生的毛刺很细小,但如果十分坚硬和尖锐,也会影响到产品安全。此外,在部件组装时毛刺可能会卡住等,降低生产的成品率。
但是,如果用普通显微镜观察立体、微小的毛刺,只可局部对焦,很难用整体图像同时对毛刺的根部和尖端进行清晰的观察,无法获取到对于查明发生原因非常重要的信息*。
与本公司旧VH系列产品的比较
4K数码显微系统“VHX系列”采用先进的光学技术和特有的观察系统,即使是立体的目标物,也可松获取并观察整体全幅对焦的图像。
采用高分辨率、大景深的镜头和4K CMOS以及环状照明,即使是延伸为胡须状的毛刺,也可从根部到尖端实施整体对焦,以4K高精细图像进行观察。
高精细图像使不良位置的整体情况一览无余,可迅速通过观察查明原因,大幅提高工作流程的效率。
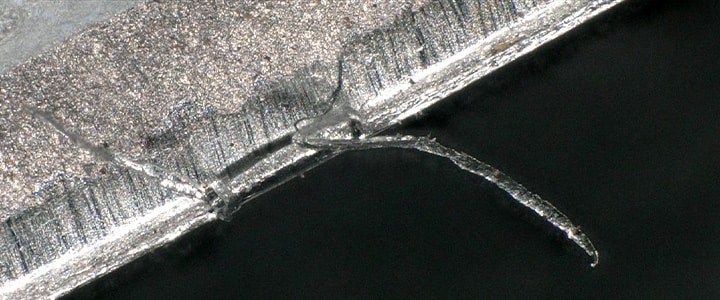
凹陷等微小不良位置的高对比度观察
由于跳屑等原因产生的平缓凹陷和细小划痕等,在金属材料表面上与背景形成的对比度较低,因此设定条件的难度很大,即使花时间去调节,也可能仍然无法顺利观察。
4K数码显微系统“VHX系列”无需手动找出条件。只需按下按钮,就可自动获取多方位照明数据的“多方位多功能照明功能”,可选择适合进行观察目的的图像。即使在选择图像后,其它照明条件的图像也会自动保存,因此无需重新放置样品,就可以不同条件进行观察。
此外,还采用全新的观察方法“Optical Shadow Effect Mode(Optical Shadow Effect Mode)”,通过抽真空等方式轻松获取接近SEM(扫描电子显微镜)的图像,连细微的凹陷也可以高对比度清晰地观察到。


可大幅提高冲压件的研发、设计、品质保证效率的4K显微系统
由于冲压件会发出金属材料特有的光泽等原因,观察难度很高,即使是熟练的操作人员也需要花费很多时间和精力去设定条件,而采用4K数码显微系统“VHX系列”后,就可用简单操作,快速观察截面和微小的不良位置。
通过融合了丰富功能的4K高精细图像,实现高水平和高效的观察,在研发、产品和模具的设计与改良、产品故障时的品质保证中发挥观察不可或缺的作用。
如需了解“VHX系列”的详情,欢迎点击下列按钮,下载查阅产品目录或随时咨询。