汽车、航空相关行业
砂型铸造的观察、分析
铸造是将金属材料在比熔点高的温度下进行溶解,流入模具中,冷却后凝固为目标形状的加工方法。下面我们将为您介绍砂型铸造的观察、分析案例。
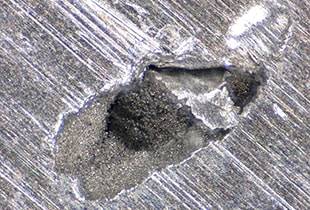
代表性的铸造方法
代表性的铸造方法如下所示。
- 砂型铸造
- 模具类型:砂型
为最古老的铸造方法,将熔融金属流入砂制成的铸模之中。虽然铸模是一次性的,但是模具制作费便宜,所以适合小批量生产。用砂型铸造制作的部件,铸模的砂粒凹凸也被转印过去,因此表面粗糙。精度也并不高。 - 压铸
- 模具类型:金属模具
用高压将熔融金属注入金属模具中的铸造方法。铸模可以反复使用,但是模具的制作费用会相对高,所以是适合于大量生产的工艺。压铸部件表面干净平整,能短时间制作高尺寸精度的铸件。 - 金属模具铸造
- 模具类型:金属模具
注入时不施加压力,借助重力注入。因此,它也被称为“重力铸造”。由于尺寸精度高,完成的铸件的机械特性出色,因此被用于制造对强度有要求的部件。 - 脱蜡
- 模具种类:石膏/陶瓷
模具中注入熔化的蜡等,以制作原型。在原型周围加入石膏或陶瓷。用炉等将石膏和陶瓷烧固的同时溶解原型的蜡。通过原型的蜡流出,形成了原型形状的空间,成为铸模。虽然铸模是一次性的,但是模具制作费便宜,所以适合小批量生产。脱蜡制作的部件表面干净平整,也可以制作高精度的铸件。
砂型铸造的种类与特点
砂型铸造的优缺点
- 优点
- 如采用木模时,初期投资便宜。
- 如采用木模时,制作时间较短。
- 形状具有一定自由度,可铸造复杂的大型产品。
- 适用于多品种、少量生产。
- 无需选择作为材料的金属(压铸仅限于铝合金、锌合金、镁合金等非铁金属)。
- 缺点
- 尺寸精度低。
- 由于是砂型,因此铸件表面粗糙。
- 由于每次需要破坏砂型,运行成本高,不适合大批量生产。
- 由于冷却速度慢,与金属模具铸造相比机械性质差。
砂型的种类
砂型的凝固方法各种各样,下述为代表性的2种砂型。
- 湿砂型
- 在硅砂中加入粘土(膨润土),利用水的粘结力凝固而成的砂型。虽然硅砂是天然产生且价格便宜,但不适合大量生产。
- 壳模
- 使用硅砂中混入热硬化性树脂(酚醛树脂)的树脂砂。因为铸模如薄贝壳状,所以被称为壳模。
因为铸模薄,表面也平整漂亮,因此常使用于汽车发动机部件等的精密铸造。虽然铸模的破坏也很简单,适合于大量生产,但是因为使用的是金属材质的模具,所以和湿砂型相比价格高很多。
砂的大小
根据砂的大小不同,铸件表面的呈现会有较大的变化。
砂粒越小,铸件表面就越平整漂亮,但是因为透气性差,所以存在容易出现气体缺陷的缺点。与此相对,砂粒越大铸件表面会变粗糙,但是其优点是由于透气性好,可以铸造出气体缺陷少的铸件。
需要根据用途,选择砂粒大小。
代表性铸造不良
代表性的铸造不良如下所示。
- 缩孔
-
- A:外缩
- B:缩孔
- a:上模
- b:型芯
- c:下模
缩孔是铸件砂眼的一种。在铸件内部产生的形状复杂的较大空洞,是由于液体变为固体时的体积收缩所产生的。
- 气孔
-
- A:气孔
- a:上模
- b:型芯
- c:下模
气孔和缩孔一样是铸件砂眼的一种。在铸件内部产生的带有圆形的空洞,是由于在铸模中进行铸造时,空气和各种气体被卷入熔融金属中而产生的。
- 开裂
-
- A:开裂
- a:上模
- b:型芯
- c:下模
开裂是指铸件表面产生的裂纹。开裂是铸造时的体积收缩等残留在内部的应力导致的。
- 流动不够
- 流动不够是指铸模中熔融金属未能完全充满,导致铸件形状不完整。
- 毛刺
- 毛刺沿着铸模的接合面(分型面)产生。其原因是由于模具精度不良、组装错误、老化导致缝隙变大等。
- 尺寸不良
- 预估铸造中的体积收缩和变形而制造铸模。由于估计量错误、模具尺寸不良、组装不良等原因而发生。
- 铸件表面不良
- 由于铸模表面的砂部分熔化,烧结而产生。
使用数码显微系统对砂型铸造进行观察、分析的案例
将为您介绍使用基恩士的4K数码显微系统“VHX系列”,对砂型铸造进行拍摄、分析的新案例。






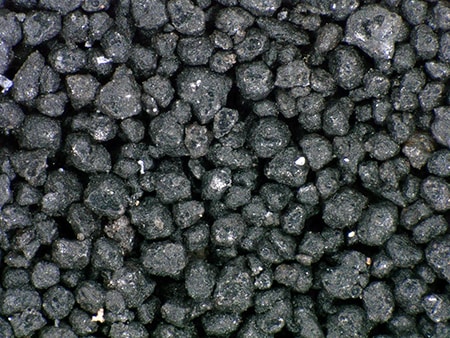








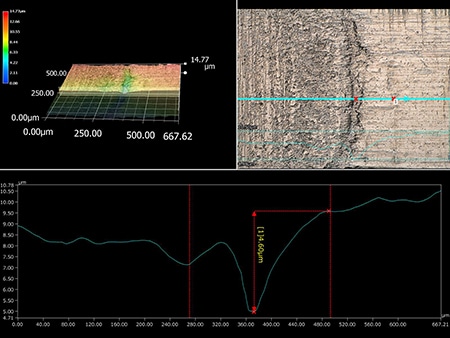
