作业的高效化
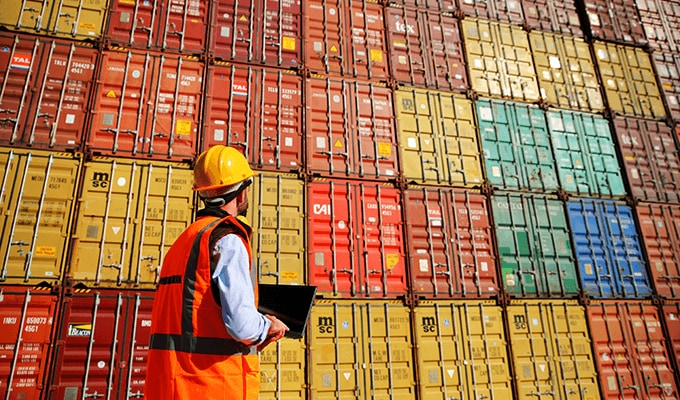
要解决物流现场的课题,必须确保从收货到发货的各个流程(包括货物流通、作业流程、信息流动等)都实现理想化。只有在实现各种作业的高效化后,才能实现“KAIZEN(改善)”的目的。下面将从“作业的单纯化”、“动线、布局的变更”、“利用物流搬送设备的自动化”这几个视角出发,说明实现物流现场作业高效化的要点。
作业的单纯化
要通过作业的高效化实现物流现场的“KAIZEN(改善)”,基本都要从流程及工序的单纯化开始入手。单纯化能够提高作业速度,减少错误,将人员配置量控制在最少的程度。但是,纯粹地将复杂的作业简化,并不能实现高效化。查明占用多余时间与劳力的作业,重新审视现状,分析改善措施及相应效果,才是作业单纯化的本质。
例如将经过拣选的商品装入箱中,交给包装负责人,换装到其他箱子里,这就是典型的重复劳动,会导致效率低下。虽然光看字面意思,就会觉得这种行为的效率很低,但在现场,长年累月的习惯经常会令人忽视作业中的异常,导致很难发现其中的浪费。高效化的关键,就是不断质疑此类习惯,剔除多余作业,通过日复一日的积累,只留下切实有效的步骤。
动线、布局的最适化
制造现场、家庭厨房或物流工序,决定使用便捷性和作业效率高低的,是现场的动线和布局。最好能够尽可能地缩短各工序间的距离,但让叉车和操作人员在同一区域活动的动线及布局设计,存在着安全方面的问题。可是如果过度重视安全性,导致散货保管区与托盘区距离过远,在移动商品及补货时就会浪费大量时间,导致效率低下。因此,必须妥善调节这些互相矛盾的要素,实现作业动线与布局的最适化。
还有一些能够立即着手实施的改善举措,例如将频繁发货的商品集中放置在货架的下方,营造让小个子工作人员也能轻松作业的环境等。有时候我们还会将使用频率理应较高的包装材料放置在物资放置处的角落里,导致要用时无法快速找到,这同样也是一种显而易见的浪费。对付诸如此类的动线及布局浪费,只需单纯地将材料移动到包装区附近即可。上面列举的这些改善点,在各种现场都随处可见,重要的通过一点一滴的累积,实现动线和布局的理想化。
利用条形码读码器的自动化、省力化
在物流现场,较大的非效率因素,就是依赖于目视的检品作业和发货单、交货单及实物确认。这样的作业不仅会造成浪费,还会引发错看、漏看等疏忽错误。如果能摒弃人力,转而利用条形码读码器来完成此类核对作业,不仅能实现高效化,还能避免误发货等错误。
利用条形码读码器的核对作业,具有目视远不能及的正确快速性,即使由经验尚浅的工作人员来使用,也能大幅降低指定作业的错误率。追求出入库作业的高效化时,条形码读码器的有效利用将成为改善的关键词。