汽车行业的视觉系统导入案例(其他案例)
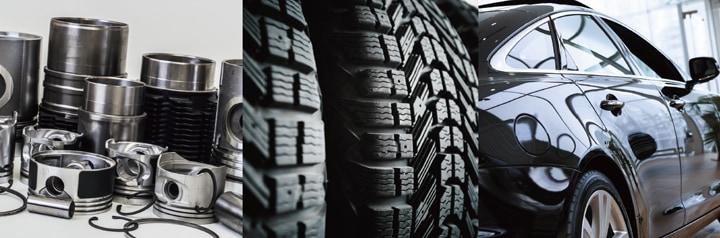
视觉系统已经被导入了汽车行业的各类检测工序中
操作面板的各类检测
检测操作面板的按钮组装错误、LCD显示不良等。传统的视觉系统会对各种标记的面积、大致图形形状进行检测,但存在类似形状误检测、大型面板检测辨别精度不足而需要使用多台相机的情况。*
只要利用XG-X/CV-X系列的轮廓形状搜索功能“ShapeTrax”,就能通过标记的轮廓信息进行辨别,实现精度更高的检测。此外,通过使用最大6400万像素的高像素相机,对于大型面板,也能用1台相机,对多个位置进行统一的高精度检测。
*与本公司CV-700 产品的比较

检测电机线的捆扎不良、焊接不良
检测电机线的捆扎不良(捆绑)、焊接不良。利用黑白相机的视觉系统,难以对线、端子、焊锡的颜色进行辨别。
而配备特色颜色抽取引擎的XG-X/CV-X系列,可以轻松准确地实现过去不稳定的线抽取处理。即使周围的照明亮度、工件光泽度发生变化,也能实现稳定检测。*
*与本公司CV-700 产品的比较

检测喷油器的组装错误
通过外径测量及颜色辨别,检测喷油器中各类部件的组装错误。传统的视觉系统会因边缘误检测,导致误判定的发生。黑白相机在部件颜色辨别方面也存在困难。*
XG-X/CV-X系列则能依靠特色的边缘检测算法,实现稳定检测,杜绝误判定的发生。自动判定最大、最小直径的趋势边缘功能,还能够削减设定工时。因其同时支持彩色相机,还能通过颜色辨别部件。
*与本公司CV-700 产品的比较

辨别安全带金具的品种
检测安全带金具的细微形状差异,进行品种辨别。在传统的目视辨别中,如果生产量增加,就会多出大量的检测工时,漏检的风险也相应升高。
导入视觉系统后,实现了全数自动检测,还杜绝了漏检。即使外观差异很小,XG-X/CV-X系列也能够对多点进行统一测量,实现切实的辨别。



辨别齿轮的不同品种
辨别齿轮直径及齿数的差异,实施品种辨别。过去在组装时只能进行目视检测,有时候在完成组装后才发现异种组装,导致成品率恶化。
导入视觉系统后,可以通过在组装工序前实施检测,有效预防组装不良。只要利用XG-X/CV-X系列的轮廓形状搜索功能“ShapeTrax”,即使工件表面及背景的亮度、颜色发生波动,也能实现稳定的检测。



辨别连杆的不同品种
通过测量连杆的全长及直径,辨别不同的品种。过去都是在投入生产线之前进行目视检测,有时候直到组装工序,才发现混入了不同品种的部件。
利用视觉系统,就能在搬运的过程中测量连杆的全长及直径,防止不同品种的混入。对于过去难以辨别的细微孔径差异,XG-X/CV-X系列也能予以测量,实现正确的品种辨别。*
*与本公司CV-700 产品的比较



检测润滑脂的涂抹量
检测润滑脂的涂抹量。过去都是借助色彩传感器进行辨别,只能进行有无辨别,对于涂抹量较少的对象,也会得出OK判定。*
而对于XG-X/CV-X系列,即使润滑脂或工件表面的色调发生波动,也能实现稳定的检测。不仅是有无判定,利用3D检测功能,还能对润滑脂涂抹量的面积和体积进行测量,辨别适量与否。
*与本公司CV-700 产品的比较



检测EGR阀门组装时的O形环有无/偏移
在EGR(Exhaust Gas Recirculation)阀门组装工序中,在压入O形环之前,确认位置偏移。过去只能依靠肉眼确认压入前的位置状况,检测难度高,缺乏准确性。*
而在检测工序中导入视觉系统后,就能实现准确的全数自动检测。只要利用XG-X/CV-X系列的轮廓形状搜索功能“ShapeTrax”,即使背景颜色波动,也能实现稳定的检测。借助超小型相机(12 mm角)和侧视镜,可以实现狭小空间内的安装。
*与本公司CV-700 产品的比较



确认热锻造金属模内的工件安装位置
在热锻造工序中,确认金属模内的工件安装位置。过去对于只有3至5秒的冲压循环,需要配备操作人员进行确认,增加了人工费。偶尔还会出现漏检导致的不良品。*
而XG-X/CV-X系列的颜色浓淡处理,可以加强原始图像的对比度,转换为清晰图像,不会受到红热金属发出的红外线影响,实现稳定、省人工的自动检测。
*与本公司CV-700 产品的比较



检测车轮的不同品种混入
检测车轮的形状差异,防止不同品种混入。传统的视觉系统难以对细微的差异进行辨别。*
XG-X/CV-X系列的轮廓形状搜索功能(ShapeTrax),却能根据边缘信息,辨别细微的形状差异,准确检测品种间差异。
*与本公司CV-700 产品的比较

辨别轮胎的不同品种
通过检测轮胎颜色标记的差异,防止不同品种混入。传统的黑白图像很难对标记的差异进行正确辨别。
使用彩色相机,就能从颜色抽取中检测浓淡,准确辨别不同品种。XG-X/CV-X系列提供的彩色相机种类很多,可以根据检测内容,选择像素数、规格、传输时间适合的相机。

检测液体密封胶(FIPG)涂抹
对涂抹在发动机、AT、机油盘等各类元件上的液体密封胶(FIPG)进行不良检测。过去该工序依赖目视检测,虽然可以判断漏涂的情况,但对于粗细等细节的判断,会因检测人员的个体差异而出现偏差。
只要利用XG-X/CV-X系列的趋势边缘宽度模式,就能对涂抹范围进行连续多点测量,正确检测粗细程度。同时具备历史图像保存功能,可以在其后检测故障部分,这也是其优势之一。



检测凸轮轴的孔洞
在凸轮轴旋转的同时,检测表面的孔洞。过去该工序依赖目视进行全数检测,不仅会漏检,还增加了人工费。
拥有线型扫描相机后,就能对圆柱状产品进行准确检测。导入视觉系统后,不仅能实现准确的全数检测,还能削减检测成本。

检测轴承的外观
检测轴承的外观不良。过去该工序依赖目视检测,人眼判断存在偏差,还会发生漏检。
导入视觉系统后,就能对大小、外轮、内轮的组装错误及外观进行准确检测。还能轻松支持多品种生产线。

检测活塞的切屑附着
检测活塞凹沟部的切屑。过去该工序依赖检测人员目视检测,人眼判断存在偏差,检测基准不统一。
利用XG-X/CV-X系统,可以通过背光照明检测凹沟部的切屑,对于细微的切屑也不会漏检,可实现定量化的检测。



切屑
检测汽车音频LCD的缺陷
检测显示器上显示的字符是否存在缺损。过去该工序依赖目视检测,不仅会漏检,还增加了人工费。
利用视觉系统实现自动化检测后,就能削减目视检测环节的成本。不仅是字符缺损,还能同时进行液晶面板瑕疵、显示字符识别等多种检测。

检测橡胶成型部件的各类外观
检测橡胶成型部件的不良。过去该工序依赖目视检测,难以准确识别不良工件。
利用“LumiTrax”功能,使用超高速相机和超高速部分亮灯照明,对目标工件进行拍摄。不会受到工件波动及周围环境的影响,对于细微不良也能实现高速稳定的检测。



检测尾灯的LED亮灯
实施尾灯、高位灯等LED的亮灯检测。过去该工序依赖目视检测,存在漏检的情况。同时无法对LED的亮度进行定量管理。
而配备特色颜色抽取引擎的XG-X/CV-X系列则不同,能够对LED的发光量轻松实现定量检测。
此外,还能够通过将检测值及实际检测图像都传输并保存到电脑中来支持可追溯性。

检测轴承脱落
检测轴承的钢珠脱落。过去该工序依赖目视进行计数,存在漏检的情况。
利用作为XG-X/CV-X系列配备的视觉系统模式之一的“斑点模式”,就能即刻进行钢珠计数,实现全数检测。

检测O形环的毛刺、缺陷
检测O形环的毛刺、缺陷。传统的视觉系统难以测量圆形的歪斜等,受其影响,检测结果也存在波动。*
利用XG-X/CV-X系列的趋势边缘缺陷模式进行检测,就能免受O形环细微圆形歪斜的影响,仅针对毛刺、缺陷等突发性变形,进行全数高速检测。
*与本公司CV-700 产品的比较

计量仪器的各类检测
用视觉系统检测计量指针的位置、角度等。传统方法中,视觉系统要测量各种位置及角度,必须进行大量复杂的运算设定。此外,边缘位置的误检测及24万像素相机的精度不足,也是问题所在。
XG-X/CV-X系列单在边缘检测一项,就配备了8种检测模式,无需复杂运算,就能实现必要的位置及角度测量。还能在31万像素到2100万像素相机中进行挑选,实现满足用途需求的高精度测量。

检测活塞环的间隙尺寸
测量活塞环的合口部。过去该工序利用接触式测隙规进行检测,但随着每年公差管理的严格化,接触式测隙规的插入情况会导致数据波动,无法实现正确检测。*
视觉系统则能在不依靠检测人员的状态下实现定量管理,轻松实现复杂的尺寸测量。对于诸如R部尺寸测量、求直线间虚拟交点等运算及多达数百种的品种,也能实现检测。
*与本公司CV-700 产品的比较

测量车身歪斜
测量车身的歪斜。过去利用变形测量器等进行测量,在准备和测量上费时费力。*
视觉系统则能通过检测激光指示器的光点位置,实现车身歪斜测量。由于检测对象是相对于基准位置的相对位置变化,可以正确测量车身歪斜。
*与本公司CV-700 产品的比较

测量驱动轴的组装平行度
测量驱动轴的平行度。过去必须借助专用的检测设备,导入费用昂贵。
XG-X/CV-X系列则能利用2台相机,分别测量轴的位置,测量平行度。通用性也很高,利用望远镜头,还能实现远距离的高精度测量。

确认车门的组装状态
检测车门部的组装精度。过去利用目视及量规等进行测量,费时费力。量规测量还存在接触的风险。
导入视觉系统后,就能削减人工费,回避接触的风险。XG-X/CV-X系列配备了专门用于几何测量的“几何测量工具”,选择几何工具后,只需用鼠标指定目标物,就能实现几何测量。
通过测量车门部的间隙尺寸,就能轻松检测出组装精度是否合格。

焊缝位置检测/定位
在弯曲加工前,对焊缝位置进行检测。过去该工序利用光纤传感器及颜色传感器实施,不同批次的表面状态存在偏差,光点检测会导致误检测的发生。*
导入视觉系统后,可以防止因误动作导致的不良品流出。利用XG-X/CV-X系列的瑕疵/污点检测模式,就能通过颜色变化情况,准确检测出焊缝位置。这样就可以不用再对每一批次的偏差进行敏感度调整。
*与本公司CV-700 产品的比较

组装车身时的定位孔感应
用视觉系统进行机械手的位置控制,实施前挡风玻璃和车门等重量部件的组装。过去对多种工件实施位置检测是一大技术难关,因此难以实现自动化。*
利用XG-X/CV-X系列的轮廓搜索、多点边缘检测,可进行虚拟圆检测、灵活搜索,支持各类工件和表面状态,实现了自动化。
还支持各类机械手厂商,无需复杂编程,即可直接连接。更配备了自动校正功能,大幅缩短启动工时。
*与本公司CV-700 产品的比较

检测齿轮的缺口角度
测量缺口的角度,控制组装环节的角度正确性。传统的测量方法,是转动工件,用光纤传感器检测缺口的有无,进而得出角度。该方法存在定位耗时,以及因部件中心位置偏移导致误检测的问题。
XG-X/CV-X系列的趋势边缘功能,能够检测虚拟圆心,以外周为基准,检测工件的中心。还能同时利用缺口进行直线检测,实现高速、高精度的旋转角度检测。

控制机械手的位置
由视觉系统进行组装、加工机械手的位置控制。该工序在过去必须借助手动示教,增加了启动工时。*
利用视觉系统,检测车身的孔洞位置,再反馈到机械手,就能实现自动化定位。即使工件位置略有偏移,也能施加补正,不再需要人工确认作业。XG-X/CV-X系列可以借助亚像素处理技术,实现高精度检测。
*与本公司CV-700 产品的比较

安全带扣的OCR
识别带扣部刻印的字符,实施品种辨别。通过字符识别,对面向国内/外的品种、左/右方向盘用的产品进行辨别等。过去该工序依赖肉眼目视检测,偶发的误检会导致不同品种的混入。由于汽车安全带属于安全部件,不允许发生不同产品混入等低级错误。
导入视觉系统后,可以实现准确的全数检测,有效杜绝不同产品混入。视觉系统检测的优势,就是能够精细呈现刻印面和工件表面的阴影。XG-X/CV-X系列提供丰富的镜头及照明选项,特色的OCR功能,能够应对刻印的浓淡变化、字符倾斜、字符大小变化等,实现稳定检测。

测量密封层的涂抹范围、体积
测量密封材的形状,检测涂抹量。传统的2D相机无法进行高度判定,无法掌握涂抹量的正确与否。
XG-X/CV-X系列可以连接超高速轮廓测量仪LJ-V系列,通过3D视觉系统,测量高度、宽度、位置、截面面积、体积等,自动检测密封材的涂抹量。还能实时补正目标物的位置偏移。
